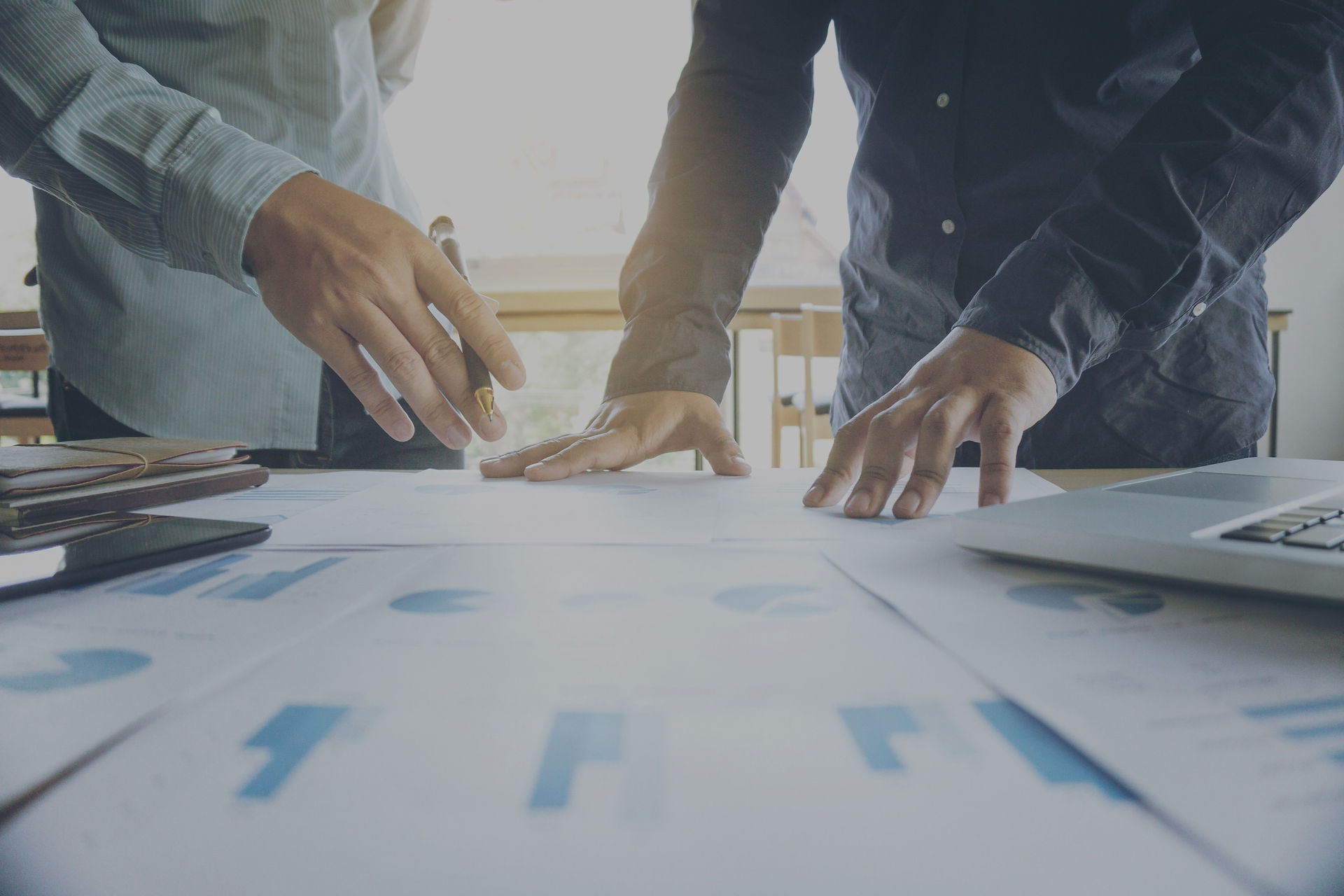

Više o metodologijama
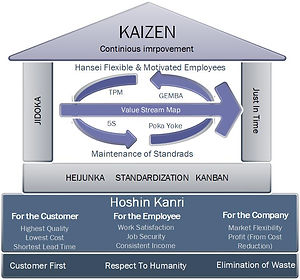


Lean Six Sigma
Lean Six Sigma metodologija nastala je "spajanjem " dijela Toyota Production System (TPS) nazvanog "Lean" i Six Sigme. Od TPS-a su uzete metode za uklanjanje gubitaka u procesima (Muri, Mura, Muda), a od Six Sigme metodu provedbu projekta (DMAIC) i statističku metodu izračuna defekata i mjerenja kvalitete procesa ("defects per milion opportunities" - "Six Sigma"). Dok se Six Sigma metoda u identifikaciji defekata (gubitaka) primarno oslanja na podatke, Lean metoda se primarno oslanja na iskustvo konzultanta u različitim industrijama i "Gemba" metodi "stvarno mjesto i vrijeme".
Metodom se rješavaju procesni problemi kod kojih je:
1. Uzrok poznat i rješenje jednostavno - tzv. Quick Win
2. Uzrok nepoznat i ima ih više, a treba ga otkriti i riješiti - DMAIC
3. Kreirati novi proces za novi proizvod (proizvodnja) - DMADV
4. Uspostaviti kontrolu na procesnim tijekom
LSS DMAIC (Define Measure, Analyse, Improve, Control) opisuju faze provedbe LSS metodologije. Svaka faza ima jasne rezultate koji su ulazni podaci za iduću fazu. Uzrok problema se "traži" pomoću Value Stream Mapping dizajna procesa i statističke metode određivanja pojavnosti defekta (Measure, Analyse), te njegovim utjecajem na konačni ishod (FMEA - Failure Mode & Effects Analysis).
Kada se otkrije uzrok problema (a on može biti ljudski faktor, metode, dobavljači, majka priroda, strojevi i alati - Ishikawa dijagram), za dizajn i provedbu rješenja (faza Improve) potrebno je iskustvo konzultanta, često odobrenje top managementa ali i iskrena suradnja svih uključenih u problem.
LSS Control faza ima za cilj uspostaviti nadzorne mehanizme nad procesom i izmjenom koju treba provesti da bi se osigurala održivost promjene i pratili učinci.
Kako se LSS metodologija danas jako oslanja na podatke iz IT sustava, u primjeni ove metode može doći do dodatnih zahtjeva na izmjenu u IT sustavima (Change Request).
Toyota Production System TPS - Just In Time - "Toyota Lean"
Toyota Production System (TPS) razvio je Sakichi Toyoda, njegov sin Kiichiro Toyoda i inženjer Taiichi Ohno 1954. godine, pod nazivom "Just In Time". Koncept je nastao na temelju Fordovog pristupa serijskog proizvodnji automobila (T-Model) iz 1909. do 1922. godine. Sve je to bilo puno prije računala i BPM-a. Model se dorađuje kroz godine i prilagođava novim tehnologijama, posebice Industry 4.0 i 5.0. Toyota je lider u tom području. Ubrzo su mnoge tvrtke u autoindustriji vidjele da Toyota proizvodi više komada, kvalitetnije i jeftinije, pa su u cijelosti ili djelomično preuzele TPS. Tako iz principima TPS-a, na zapadu nastaju broju brojne metodologije Lean, Agile, Balanced Scorecard...
Toyota Production System (TPS) je cjelovit pristup svim segmentima upravljanja tvrtkom, a temelji se na filozofiji "Na prvom mjestu korisnik", "Respekt prema čovječanstvu - posebice zaposlenicima" i "Uklanjanje gubitaka -smanjenje troška" i maksimalnoj standardizaciji proizvodnog procesa ili isporuke usluga.
TPS promatra proces kao vrijednosni lanac (Value Stream). Da biste automatizirali procese (Industry 4.0,) ili da biste primijenili Robote ili Kobote Industry 5.0 svaki procesni korak mora biti maksimalno standardiziran i resursno optimiziran (Heijunka). Ono što nije moguće standardizirati ili se događa neočekivano rješava kompetentan i motiviran zaposlenik (Poka Yoke, TPM), čime se osigurava najbolja kvaliteta i pravovremena reakcija u takvim slučajevima. TPS ovaj pristup zove Jidoka "Automatizacija s ljudskim dodirom". Druga velika prednost TPS-a je Kanban pristup procesima. TPS Kanban procesni pristup u realnom vremenu pretpostavlja PULL procese, što znači da svaki naredni proces uzima onoliko od prethodnog i od resursa (ugradbenog materijala) koliko je u stanju isporučiti. Ovim procesima upravlja pomoću Kanban "pull", "production" i "signal" kartica. Kanban model upravlja procesima omogućuje samo-usklađivanje (automatizaciju) cijelog lanaca vrijednosti do krajnjeg korisnika i minimalne zalihe.
U svakoj proizvodnji ili isporuci usluga događaju se neočekivani problemi, pa tako i u Toyoti. TPS nudi rješenje i za ovakve situacije - Gemba / Genchi Gembutsu ("Stvarna lokacija, stvarno vrijeme i stvarni problem") odnosno TPM (Total Production Mainatence). Gemba kaže da se problem ne može rješavati iz ureda, nego tamo gdje je nastao, a TPM kaže da ga rješava onaj zaposlenik koji radi na stroju, uređaju ili alatu, odnosno inicijativu za vođenje rješavanja problema preuzima onaj djelatnik koji je izravno ugrožen problemom. Tako na primjer djelatnik koji poslužuje neki stroj ili radi s nekim alatom, treba ga znati i popraviti u većini slučajeva za što ima na radnom mjestu sve potrebne dijelove i alate. Na taj način se stvaraju ogromne uštede na održavanju, smanjuje vrijeme čekanja (gubici proizvodnje), stvaranje zaliha zbog zastoja i povećava zadovoljstvo korisnika. Ove uštede su daleko veće od troškova većih plaća za kvalitetne, lojalne i motivirane zaposlenike. U skladu s tim TPS predviđa evaluaciju zaposlenika na principima samo-evaluacije (Hansei - Self Reflection i 5S) sposobnosti u skladu s gore navedenim principima iz kojih nastaje prijedlog razvoja svakog zaposlenika, napredovanje i nagrađivanje. Tako svaki zaposlenik o svojoj plaći i poziciji odlučuje sam.
Da bi cijeli sustav funkcionirao Toyota je u okviru TPS-a razvila planiranja i postavljanje ciljeva Hoshin-Kanri. Hoshin Kanri predviđa podrazumijeva da je sve prethodno navedeno uspostavljeno. Na taj način poslovni plan je vjerodostojan, ostvariv, predvidljiv, a pomoću PDCA (Plan Do Check Act) i kontroliran u stvarnom vremenu pa ga je moguće i promijeniti ako se tržišne okolnosti promijene.
TPS Je sveobuhvatna metodologija koja djeluje na sve segmente upravljanja operativnim učinkovitosti tvrtke. Primjenjiva je na sve industrije, a ne samo na proizvodnju. Na temelju našeg iskustva primjene u Hrvatskoj najbolji rezultati su ostvareni u servisnoj (isporuka usluga), IT industriji (Service Desk, 2.3. level support), građevinskoj industriji i proizvodnji.
Kayocera Amoeba Management metodologija - "Management by All"
Kayocera Amoeba Management metodologiju razvio je Kazuo Inamori, vlasnik i osnivač Kyocera korporacije. Nema široku primjenu u svijetu, jer računovodstveni koncept drugačiji od standardno prihvaćenog na zapadu. Uz Kyoceru, metodologiju još primjenjuju KDDI (Japanska Telekomunikacijska kompanija), Japan Airlines, Capcom (softverska tvrtka za razvoj računalnih igrica), i još neke tvrtke u Japanu.
Smatramo da će ova metodologija imati izuzetan potencijal u budućnosti posebice u poslovnim modelima akvizicija i outsourcinga (izdvajanja pojedinih dijelova kompanije) u posebne poslovne subjekte neovisno o vlasništvu.
Amoeba Management postavlja organizacijske i računovodstvene temelje tvrtka na 3 principa: (1) Svaka interna organizacijska jedinica (divizija, sektor ili niža) je "profitni centar" i ima "vlastiti" računovodstveni sustav, odnosno odgovorna je da posluje profitabilno (ameba). (2) Drugi princip je da se među zaposlenicima bira Lider (menadžer) onaj koji posjeduje sposobnosti vođe, i dalje se razvija u smjeru menadžmenta. (3) Management by All princip koji omogućuje svakom djelatniku da sudjeluje u upravljanju svojim odjelom (amebom).
U praksi ima primjera koji slično i vrlo uspješno funkcioniraju kao na primjer brodski transport, različiti proizvodni pogoni iste korporacije rašireni po cijelom svijetu. Razlika je u tome što Ameba Management ide dublje s primjenom sve do razine odjela. Važno je da se lideri biraju iz postojećih zaposlenika, a biraju ih zaposlenici samo, jer o izboru lidera ovisi njihova plaća, budući razvoj i napredovanje. Svaka ameba dijeli ono što je uprihodila.
Ameba Menadžement vertikalnu organizaciju (silose) pretvara u mrežnu organizaciju (horizontalnu) gdje je uloga centralno menadžmenta korporacije osigurati najefikasniju integraciju ameba, podršku njihovom poslovanju i nadzor profitabilnosti i usklađenosti.
Ameba Menadžement je primarno namijenjen industrijama koje mogu proizvoditi različite proizvode ili isporučivati usluge neovisno od drugih - imaju zatvoreni vrijednosni lanac (jedna zrakoplov, jedan kamion, jedna željeznička kompozicija, jedan brod ili na primjer dio tvrtke koji proizvodi samo hladnjake). Svaka računovodstvena jedinica isporučuje cjelovitu uslugu ili cjelovit proizvod, međutim svaki odjel također proizvodi cjelovit poluproizvod ili isporučuje dio cjelovite usluge koji se može kupiti i na ražištu. Na taj način korporacija stvara konkurentsko okruženje internim organizacijskim jedinicama i motivira ih na tržišno ponašanje i poslovanje. prednost ovog pristup je smanjenje administrativnih i IT troškova i overheada, jer je svaki lider ujedno i operativna djelatnik neke amebe.
Agile Management
Agile Management metodologija, posebice Agile/Scrum koji se koristi u IT industriji za razvoj softvera je također nastala iz Toyota Production System metodologije. Biti agilan znači biti brz, dinamičan, samostalan, odgovoran i fleksibilan. Tako u IT jedan Scrum tim razvija određenu funkciju u softveru koju korisnik može prepoznati, i tako ciklički cijeli softver. Ideja agilea je rascjepkati veći projekt u manje funkcionalne cjeline kojima se može odrediti zahvat (sprint ili story), trajanje izrade, testiranje i isporuka. Obično je trajanje jedne isporuke 2 tjedna.
Ovako unaprijed definirani rok isporuke određuje i sadržaj koji je moguće u tom periodu "proizvesti". Ovom standardizacijom postiže unaprijed zadana dinamika isporuke kao u proizvodnji (Heijunka - Load Leveling) i Takt Time isporuka. Jedan od principa agile/scrum metodologije je i da korisnik ne mora dati detaljnu specifikaciju, već tim treba prepoznati potrebu, kreativno ponuditi rješenje koje rješava korisnički problem. Ovaj pristup traži kreativnost agilnog tima. Zato svaki tim ima tehničkog voditelja (Scrum Master) i Product Ownera koji bi trebao razumjeti i prenijeti na prihvatljiv način očekivanja korisnika timu.
Glavna karakteristika svih gore navedenih metodologija je trajanje jedne faze isporuke, proizvodnje u kreiranju konačnog proizvoda (tzv. Takt Time) u vrijednosnom lancu do korisnika. Pogrešno je povezivati Takt Time s "normom" jer se normira aktivnost, a ne isporuka. TPS umjesto normiranja koristi standardizaciju na razini isporuke i load leveling (upravljanje opterećenjem) Heijunka. Zato treba biti oprezan u primjeni ovih metoda jer neće dati rezultate ako se pogrešno ili selektivno primjene.